Practical Materials Planning Strategies for Specialty Contractors
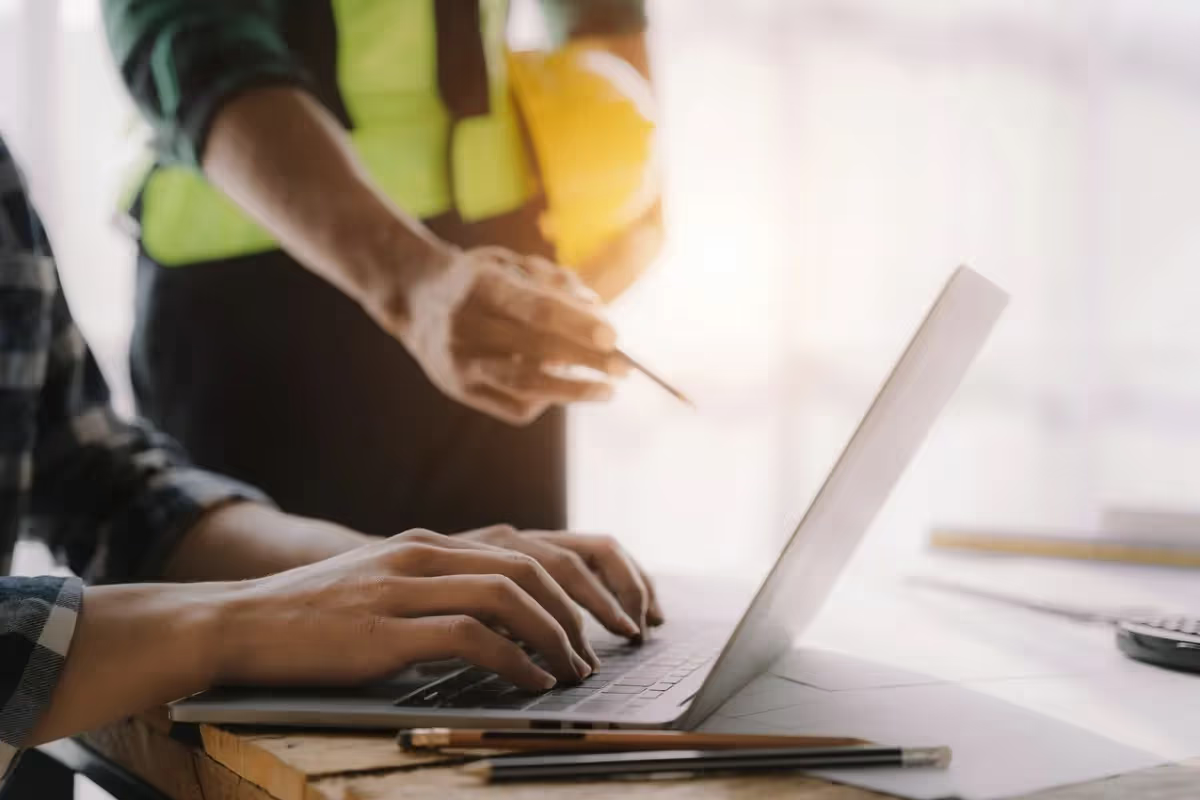
Every contract job begins with a plan, but there can be expensive setbacks when the process lacks organization and consistency. Effective construction planning involves a well-structured bill of materials (BOM) to avoid cost overruns, excess inventory, and last-minute orders that put job schedules at risk.
Let’s break down the most important factors to consider in materials planning to increase efficiency and reliable outcomes.
Does your BOM set you up for success?
A BOM is the foundation of construction management. It should integrate learnings from past projects with estimates for the job at hand to ensure your team is prepared to handle realistic deviations. It should also provide your team with precise visibility into material spend and usage throughout the project, allowing you to identify potential risks before they become bigger problems.
Taking steps to optimize materials planning will give your team a competitive edge. When construction plans are well informed, they mitigate risks in execution. To determine if your BOM is helping your team achieve their potential, ask a few questions.
Answer these 8 questions to assess your BOM.
1. Can you easily create a BOM from estimates or project drawings?
2. Are material lead times and supplier reliability factored into the BOM?
3. Does the BOM consider potential cost-saving opportunities without compromising quality?
- Utilizing warehouse inventory to avoid unnecessary purchases
- Spotting bulk order opportunities for discounts
4. Does your BOM include necessary information?
- Material/part name
- Material/part brand
- Material/part numbers
- Estimated quantities
- Estimated prices
- Vendor name
- Phase code
- Cost codes
5. Are you updating your BOM in real time to track spending and purchasing decisions?
6. Do data and analytics play a role in your job planning?
7. Do you know what was delivered on time or damaged?
8. Can you see who on your team made every request and purchase?
If you answered no to any of these questions, your job outcomes can benefit from better planning. As one element of quality management for construction projects, a thorough bill of materials can boost efficiency while maintaining high standards, healthy margins, and strong relationships.
What does great materials planning look like?
Building a better BOM is essential to avoiding costly mistakes and delays. It’s the difference between getting the job done and getting the job done right. Each component of the process will strengthen your construction planning, and it starts with your BOM.
Use the best information you have to build your BOM and improve your planning.
You don’t have to be operating at the highest level with a materials procurement platform to benefit from complete, accurate information. Even if your BOM is simply a spreadsheet, it can still provide opportunities for you to optimize material purchasing for future jobs. Just make sure to update the file throughout the job, tracking the differences between planned and actual spend, usage, delivery fulfillment, and so on.
Organize your BOM with important material information.
Your bill of materials should be specific and standardized; this will make it efficient to reference and functionally enhance your procurement process. It should include the preferred brand and corresponding material/part number of each item, quantities, prices, job phase, and cost codes. These additional details will create endless insights for better planning.
Assess your warehouse inventory.
If you purchase materials without knowing what’s on your warehouse shelves, job waste is inevitable. A dependable operation or software for inventory tracking is one of the easiest ways to improve planning.
Identify materials that you can buy in bulk at different phases of the job.
Bulk discounts can lead to substantial savings when purchasing materials in volume. By referencing warehouse inventory, an organized BOM with required quantities for each job phase, and data from historic projects, you can make informed decisions that keep the project within budget.
Provide key team members with visibility into your BOM.
Delegation is a part of managing any project, and it’s necessary to scale operations. Ensuring that key team members have access to an organized BOM will empower them to make informed decisions quickly. There are multiple ways to achieve this, including cloud-based file sharing and materials procurement software designed for contractors.
Update your BOM throughout the job to track job progress.
A well-planned BOM should be a living document, and keeping it up to date throughout the job is crucial. Establishing a schedule for checkpoints to assess progress will pay off with smarter purchasing decisions. Software can also be useful for updating the BOM in real time without additional administrative work.
Step up your construction plan.
Procurement doesn’t end with materials planning. To improve the efficiency and success of your construction projects from start to finish, read 7 Steps to Better Procurement for Specialty Contractors.
Related posts
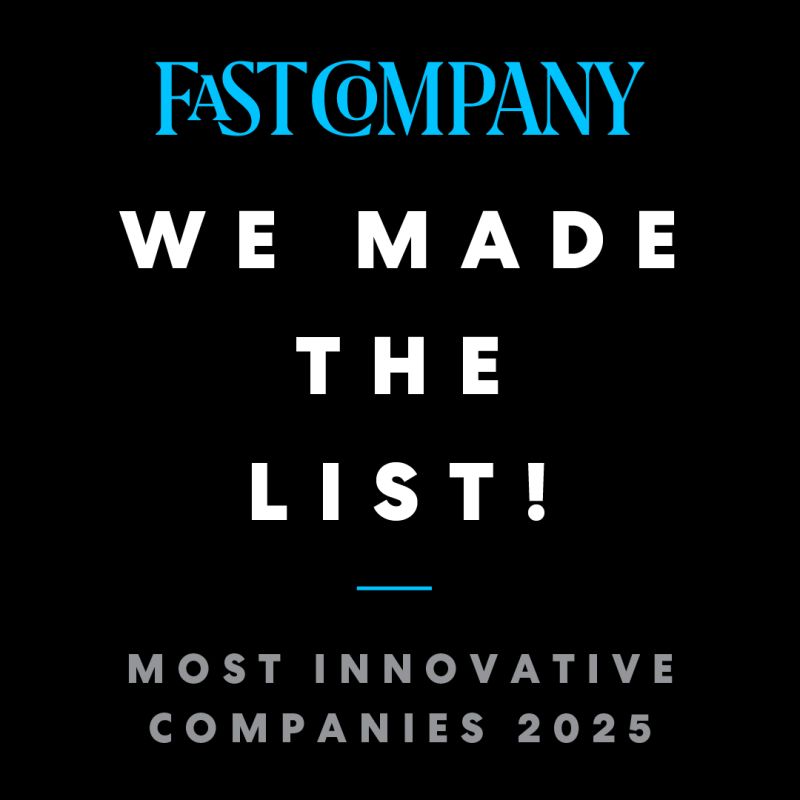
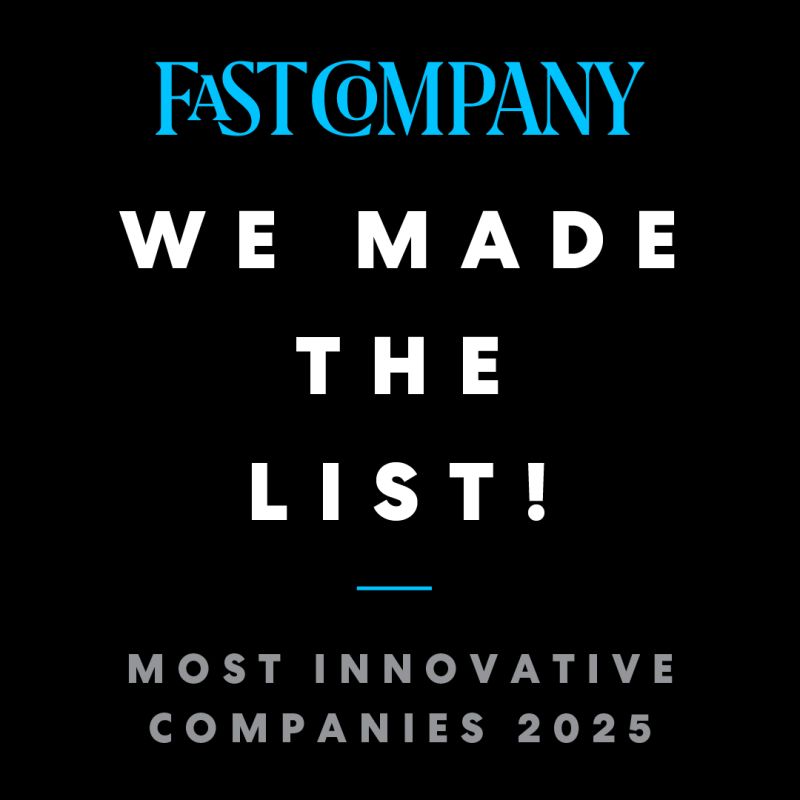
Kojo Named One of Fast Company’s Most Innovative Logistics Companies of 2025
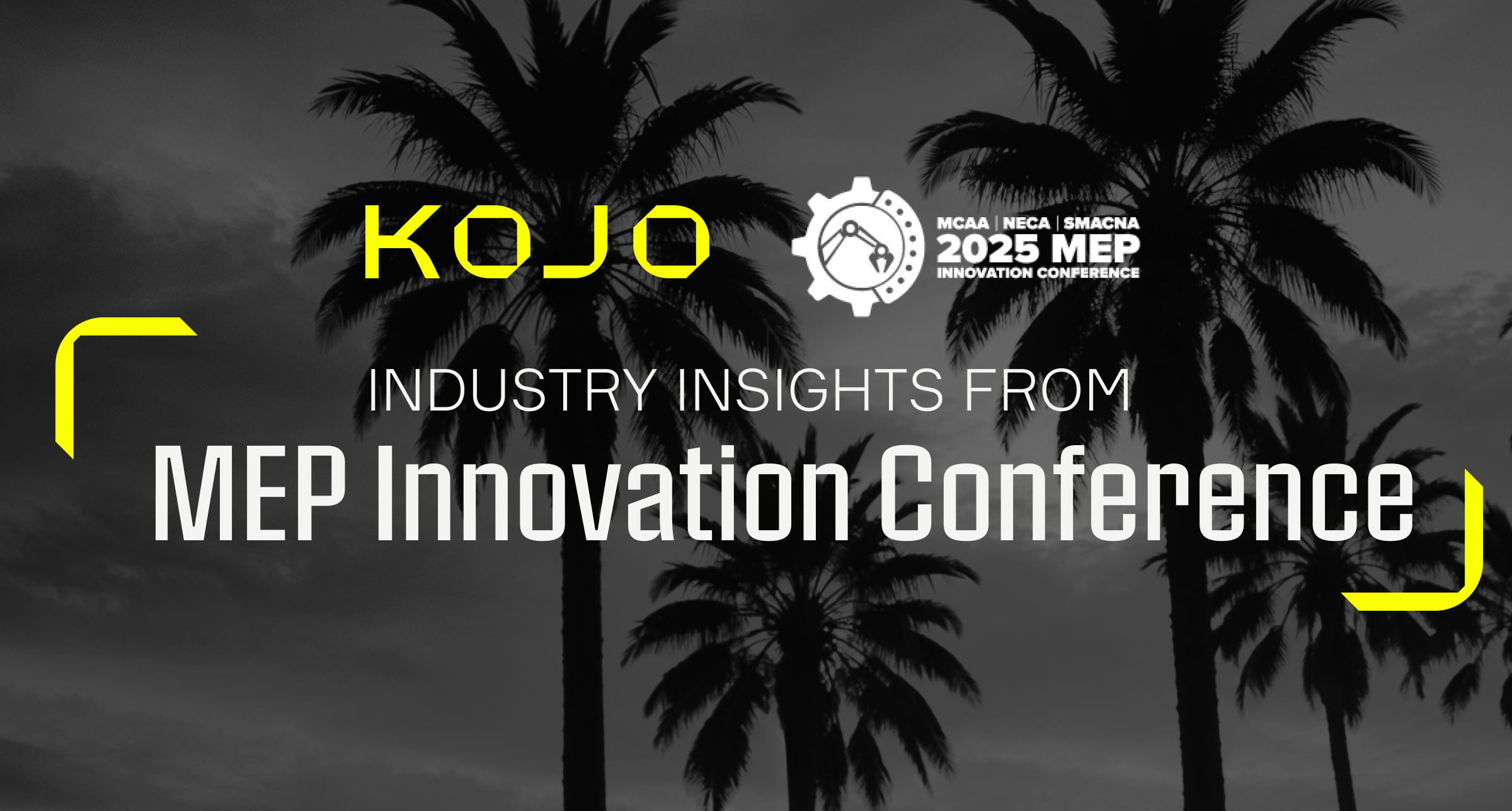
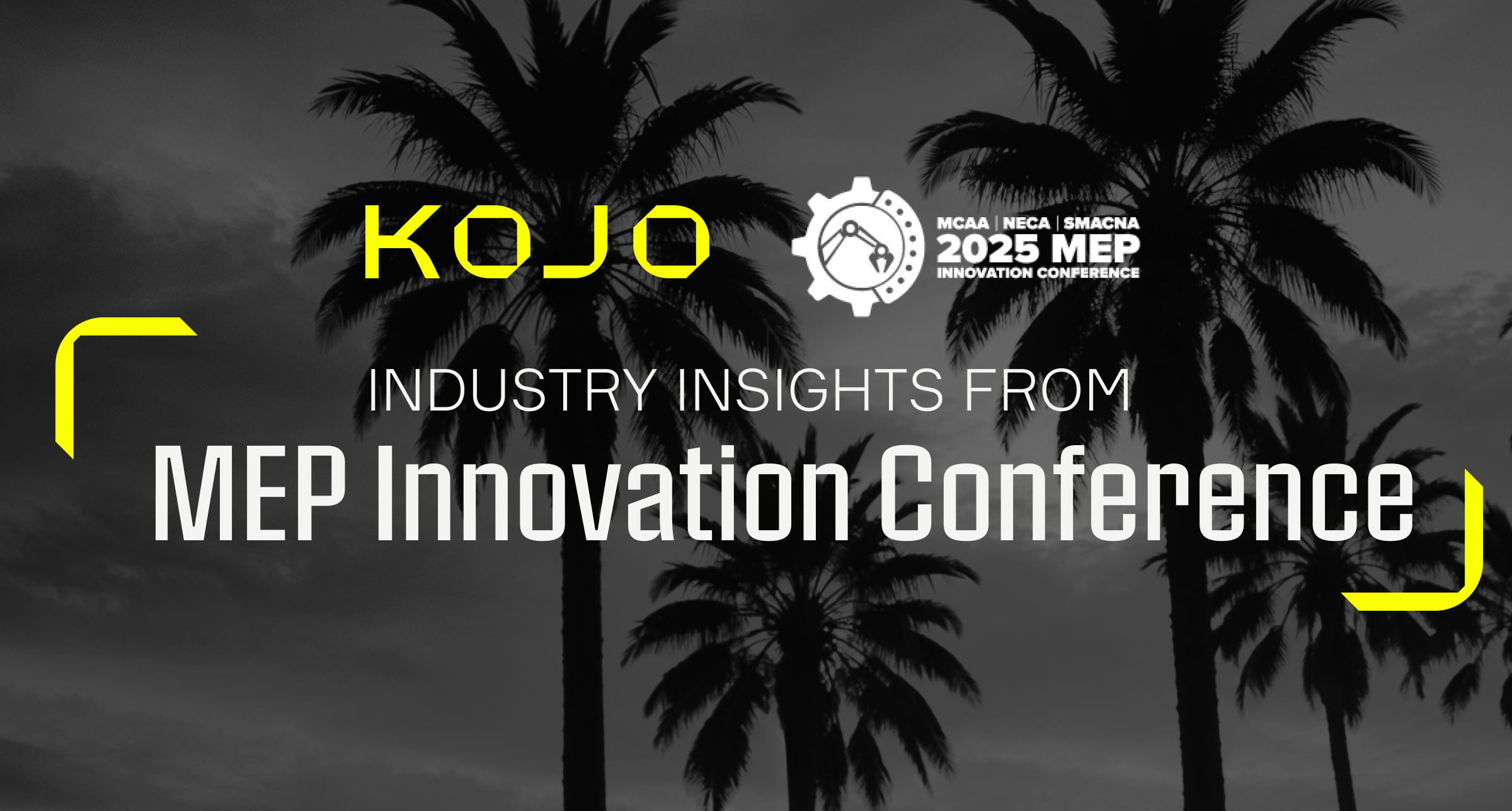
Industry Insights From MEP Innovation 2025: Trends We Observed
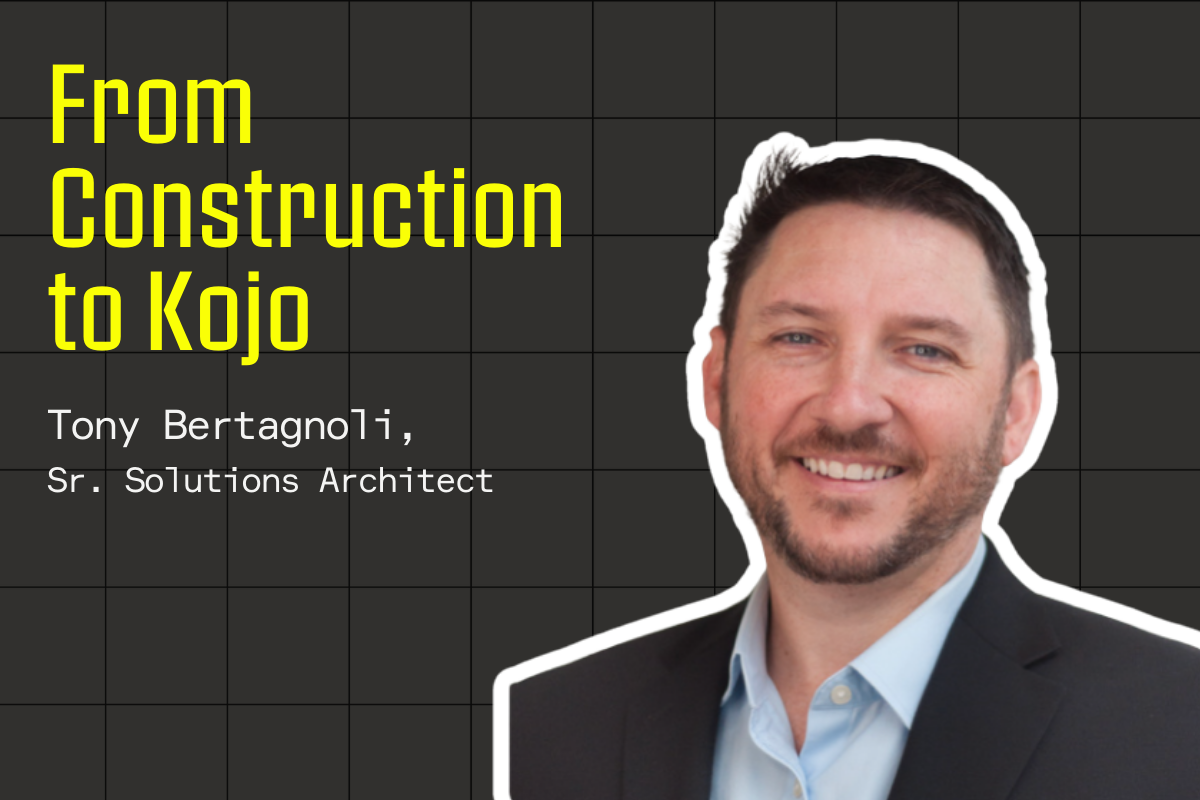
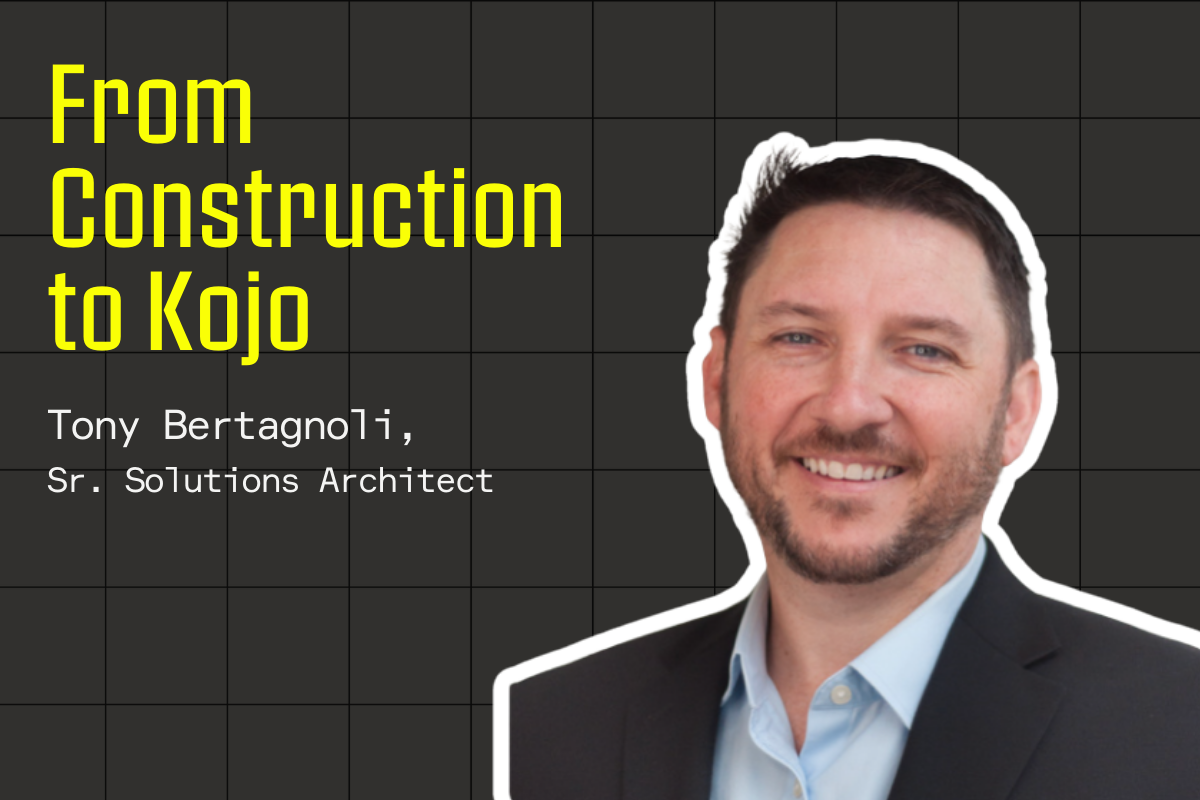