Material prices are out of hand but there are ways to control project costs
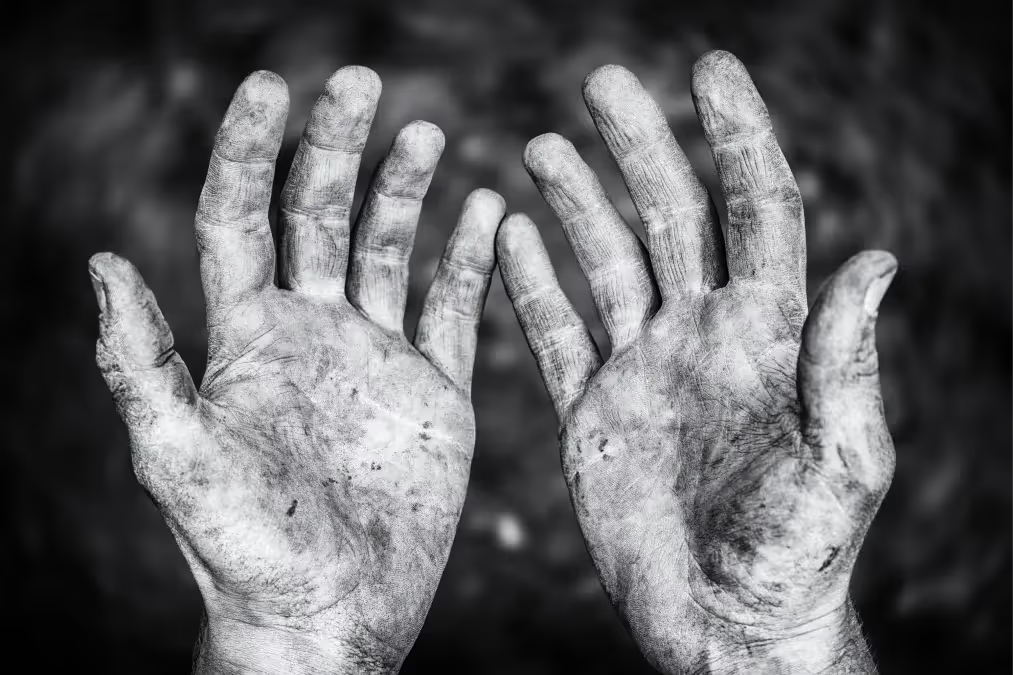
Materials Management - The Key to Controlling Project Costs.
A global pandemic and fractured global supply chain, combined with a trillion-dollar US infrastructure bill has significantly increased demand for construction work while simultaneously drying up the supply of materials. As a trade contractor, you assume the risk for material-related issues and as a result, you’ve been hit the hardest with an endless stream of backorders, unpredictable lead times, and all-time high materials prices. On top of this, labor is scarce and the solutions for addressing the labor problem may take years to bear fruit. Now more than ever, your margins are at risk. But the kicker is that all of these issues seem entirely out of your control.
Yet these pressures have not stopped project owners from expecting competitive prices. So to win work but also protect your margins, you must identify and improve the factors that are within your control.
The concept of project control is not new to construction. For years, the industry has implemented processes to gain better control over construction projects. The basic principles of project controls - better planning, risk management, forecasting, process management, documentation, and data analysis and reporting - can be summarized as “thinking ahead, improving documentation and visibility, and streamlining processes without introducing risk.” Simple enough, right?
Some elements of project control are just baked into the way we do things in our industry - planning meetings, progress documentation, scheduling, and project management are inherent elements of any construction job. And most contractors these days have implemented project controls around labor management and general field documentation, leveraging construction management solutions that have proliferated in recent years. However, one potential area of control that has so far been neglected by technology (and therefore by many contractors) is materials management.
Most contractors manage materials through a hodgepodge of paper, email, phone calls, and spreadsheets. And the issues with an outdated process extend well beyond frustration for your internal teams. A manual, multi-step, prolonged materials management process leads directly to productivity losses in the field and also for your administrative staff, which means both your project and overhead budgets take a hit. One study found that outdated materials management processes result in average productivity losses of 2 weeks per year for field staff, and 7 weeks per year for office purchasing staff [Electrical Contractors: Materials Purchasing Benchmark Report, 2022].
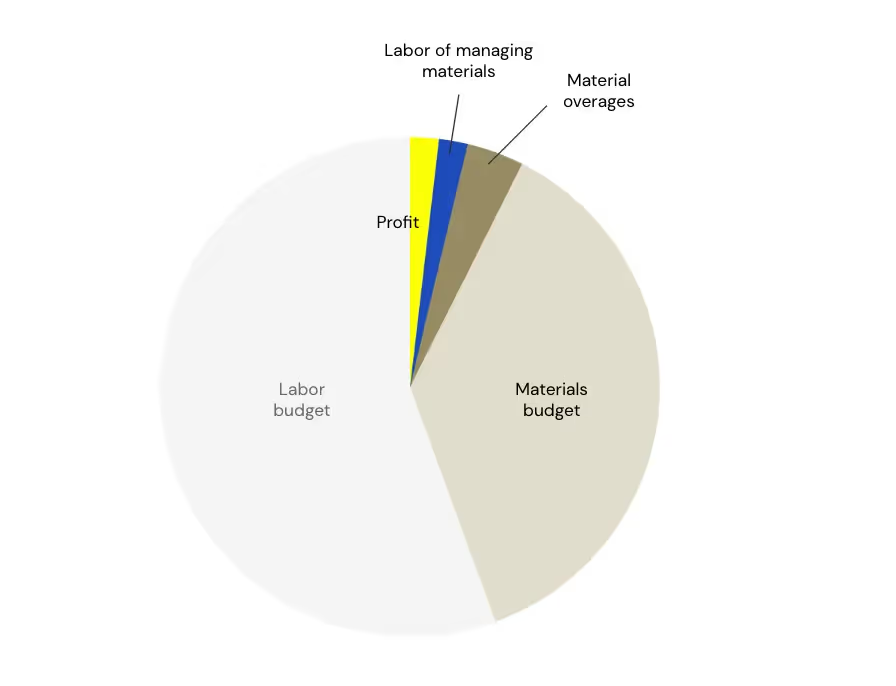
A cumbersome materials management process also encourages your team to skip simple steps that could yield direct material cost savings. For example, a purchasing manager who is already overburdened with simply transcribing daily “ASAP” field requests likely won’t have time to do optimization tasks, such as price shopping, splitting out POs to optimize pricing and availability for each line item, or carefully matching invoices to POs and proof of delivery. By skipping steps, businesses miss opportunities to reduce direct costs. For example, contractors typically inadvertently overpay by as much as 10% due to invoice errors [Materials Management Best Practices Outside of the Gate, NECA 2022] - that means you’re paying 10% extra because you don’t have time or resources to optimize your materials management process.
A fragmented materials management process also keeps your team in the dark on key information like pending orders, order status, and warehouse inventory, which leads to mistakes, duplicate orders, and more wasted time as people try to gather basic information. Ultimately, these mistakes can add up.
Low productivity, lack of optimization, and limited visibility all point to a materials management status quo that totally misses the mark in terms of control. The materials management process is a prime target for gaining more control and therefore protecting your margins. And the way to gain greater control in materials management should be obvious - technology. Even construction’s historically tech-averse workforce is now familiar with using mobile and web apps to share information instantly. Yet materials are still being handled the same way they were 20 years ago. In order to take control over materials management, the industry needs to adopt technology solutions that will streamline and optimize the materials management process.
For contractors who embrace a better process for materials management, the results will be better control - which means direct material cost savings, a more productive workforce, and improved profit margins..
Kojo is a one-stop-shop for trade contractors to consolidate their entire materials management process. By connecting the field, office, warehouse, accounting teams, and vendors, contractors gain visibility into real-time materials spending and usage, increase labor productivity, and optimize material costs.
Related posts
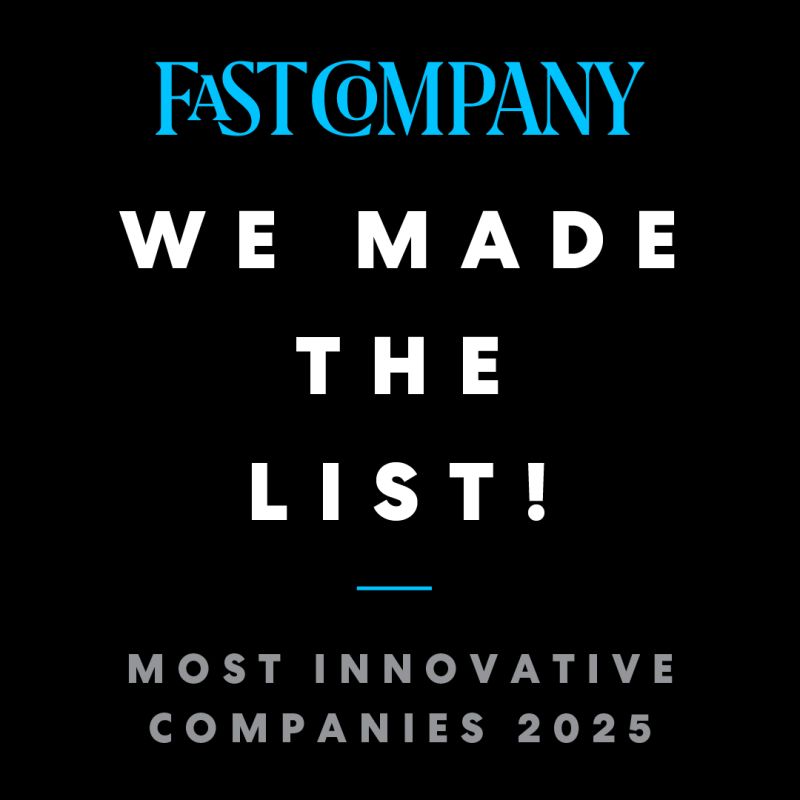
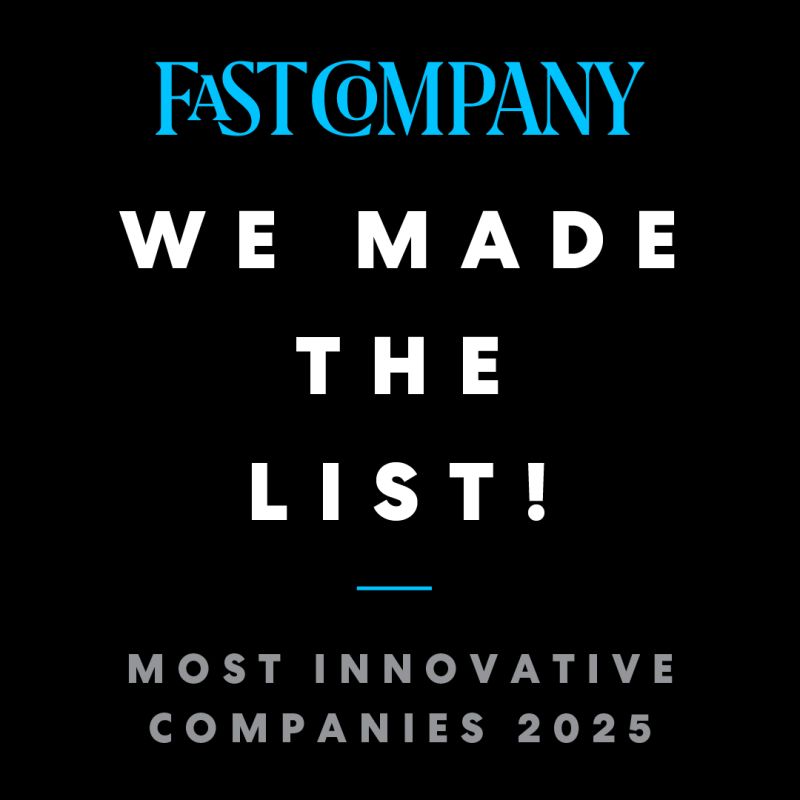
Kojo Named One of Fast Company’s Most Innovative Logistics Companies of 2025
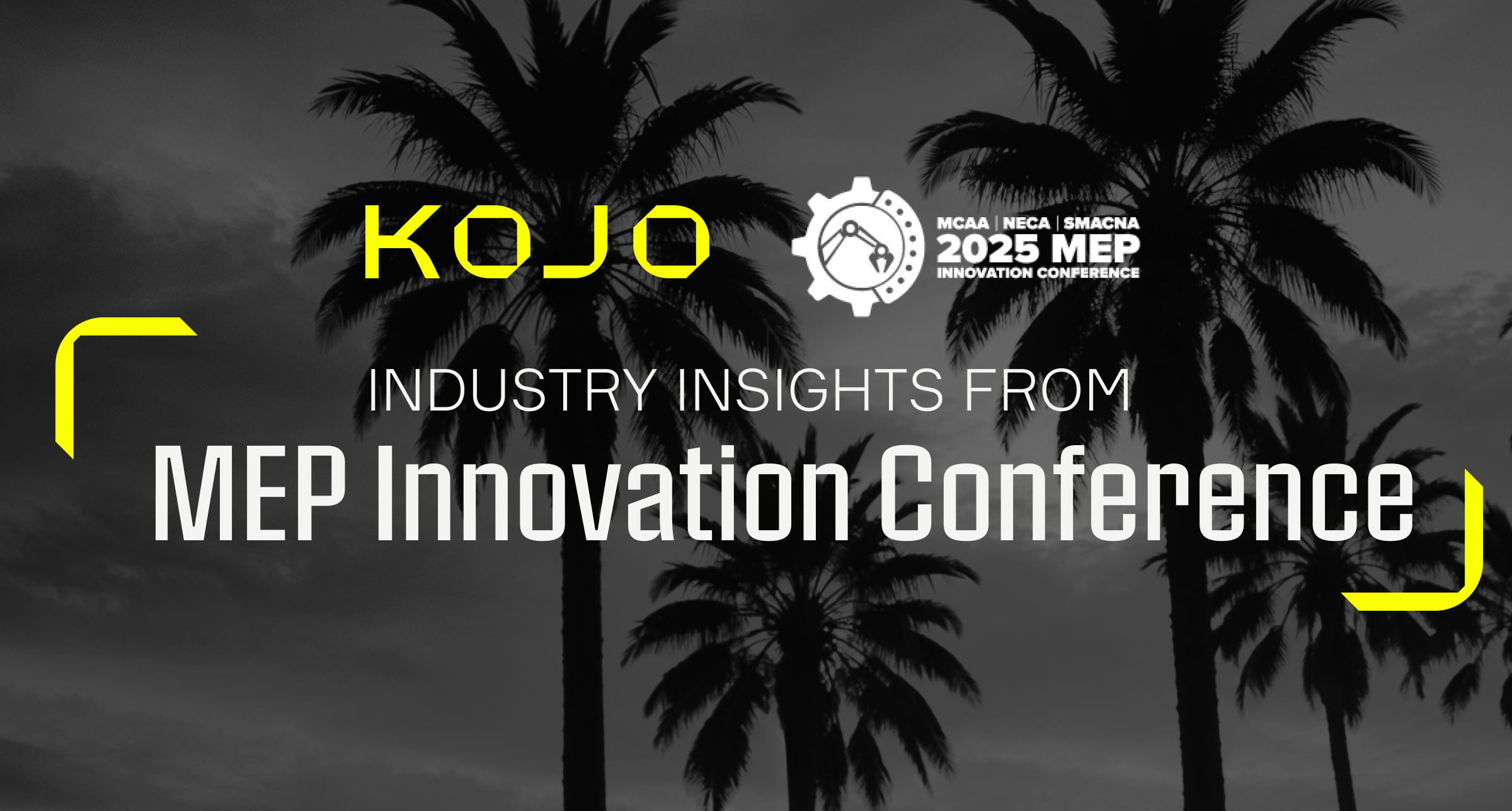
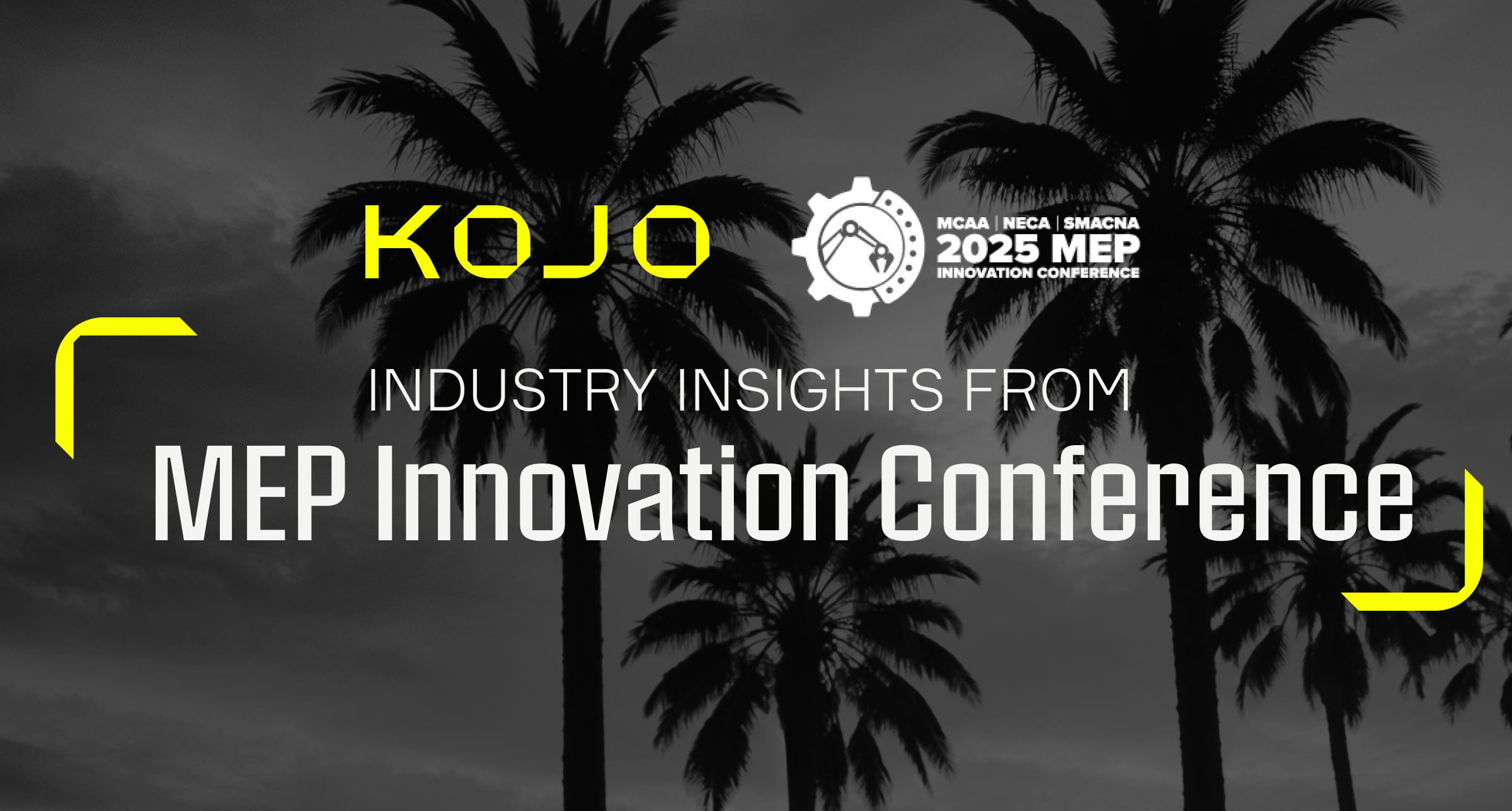
Industry Insights From MEP Innovation 2025: Trends We Observed
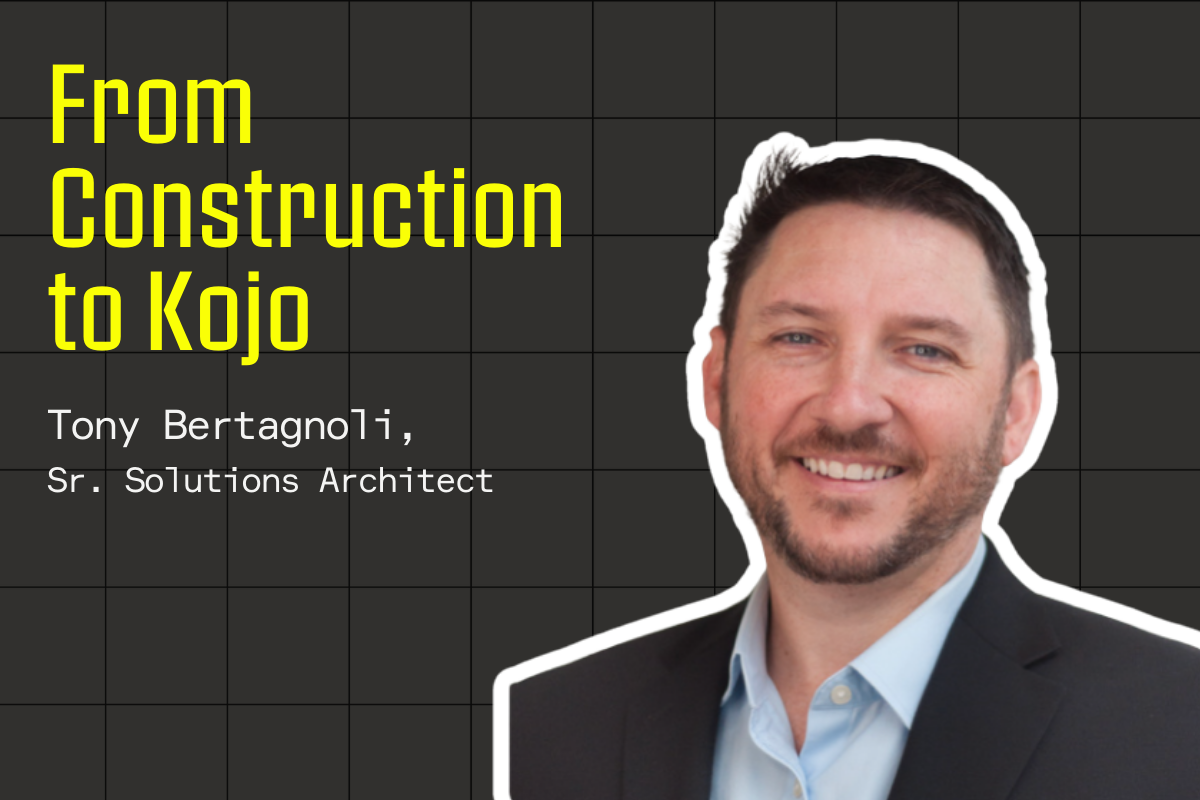
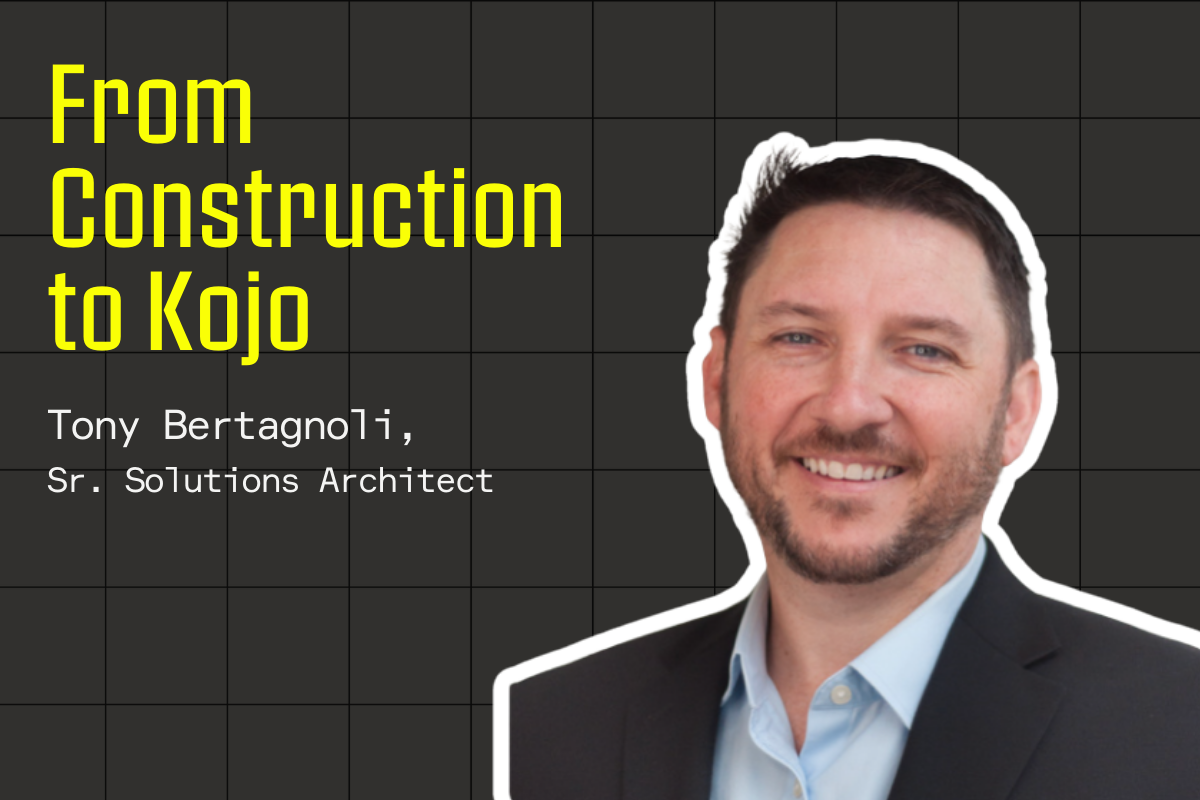