3 Reasons Why Visibility Into Your Warehouse Leads to Successful Jobs
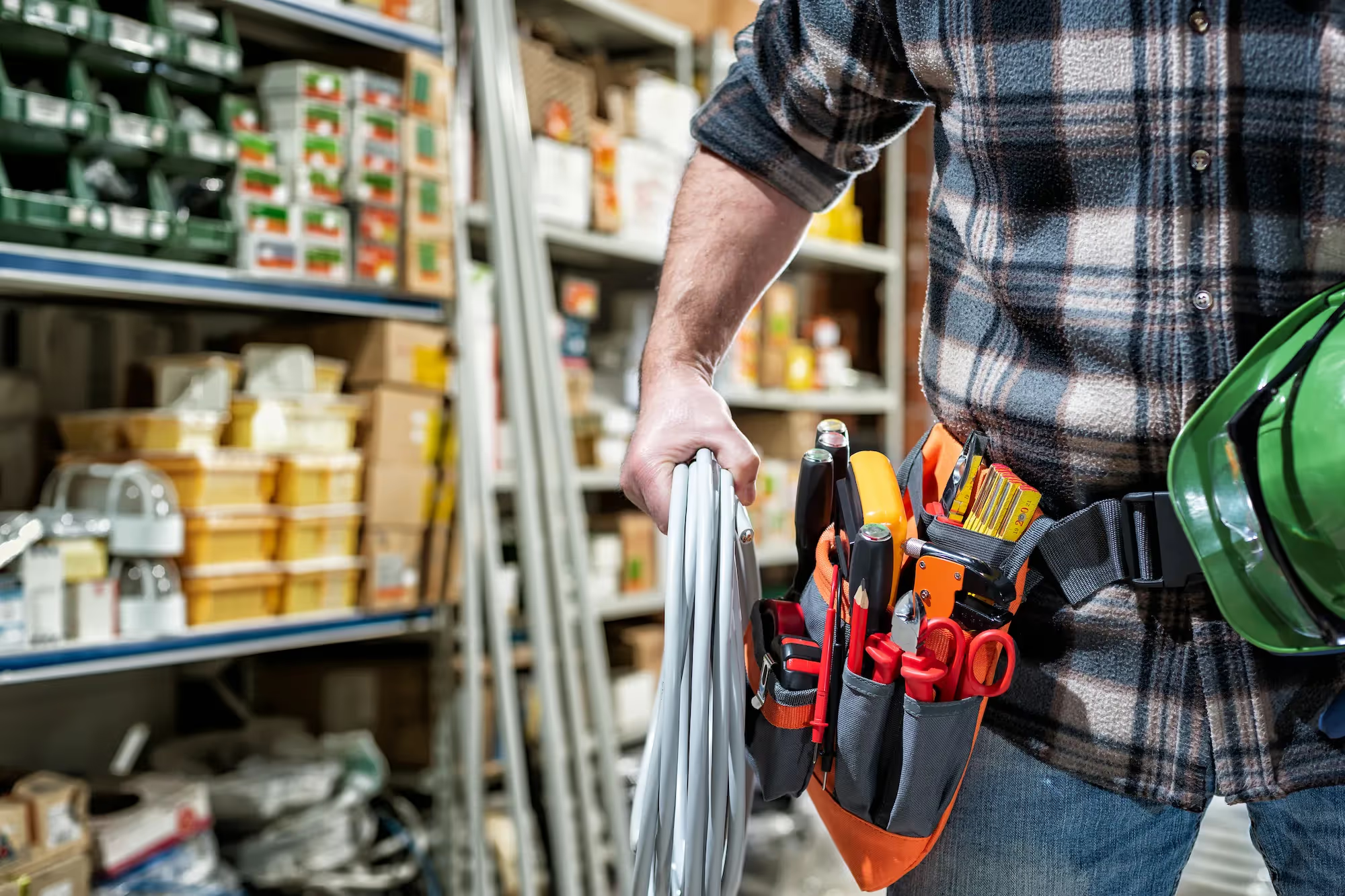
Worldwide, the construction market is facing considerable pressure with materials scarcity and volatile pricing. To combat these, many companies are turning to their warehouses for answers. When it comes to purchasing and managing materials, keeping your team aware of what materials are available in your warehouse is crucial. Let’s break down 3 reasons why ensuring your team’s visibility into your warehouse inventory can lead to successful jobs.
Unlock material cost savings
Part of having a successful job is ensuring that you keep material costs low and within budget. You can help keep these costs down by improving your team’s visibility into what’s available in your warehouse.
As the field is creating requisitions, you can cut down on double ordering if the field already knows what they have allocated for them in the warehouse. By seeing exactly what they need, foremen can get these materials sent directly to the job cutting back on the need to send new purchase orders to vendors for materials that are already on hand.
In addition, sending last-minute orders to vendors can be very expensive. Rush orders incur additional higher fees, like shipping, that can put your project budget at risk. This can be avoided by making sure you order the materials you need ahead of time and inform teams of how to find and request them.
Stay ahead of supply chain issues
Since 2020, the construction industry has suffered a tighter squeeze on the materials supply chain. The National Association of Homebuilders (NAHB) reports that in 2021, “more than 90% of builders reported delays and materials shortages.” From materials consistently being out-of-stock to lead times that can span months, it’s imperative you have options that mitigate against backorders to keep you ahead of the curve. Keeping your warehouse stocked with materials you use frequently is one effective way to do this. Your inventory management and purchasing teams can keep a close eye on these material stock levels and ensure they provide enough time to restock for the field. With the combination of knowing what’s available in your warehouse with a few clicks of your mouse and quickly ordering materials ahead of time that will be needed, tech-savvy contractors are discovering that they can win more bids and keep jobs on track. They are more confident that they’ll have the materials they need for the jobs. Leveraging your internal warehouse for this purpose brings peace of mind and a sense of efficiency for getting materials where they need to go. Have less waste at the end of a job.
{{banner-1}}
According to Science Direct, as much as “30% of all building materials delivered to a typical construction site can end up as waste.” Collecting, transporting, and restocking leftover materials comes at a cost to contractors, leading to many materials being thrown into the dumpster. When visibility into warehouse inventory expands across your team, it opens up downstream benefits that can reduce waste. Tracking what materials are restocked to the warehouse gives purchasing teams the ability to designate materials for the next job. Implementing a workflow that updates inventory stock levels in real-time keeps materials flowing in and out of the warehouse smoothly.
{{banner-2}}
As you expand your construction business and take on more jobs, having a warehouse with transparent inventory and stock levels keeps teams productive overall. Check out inventory management solutions with Kojo that can assist you in optimizing your budget and achieving success.
Related posts
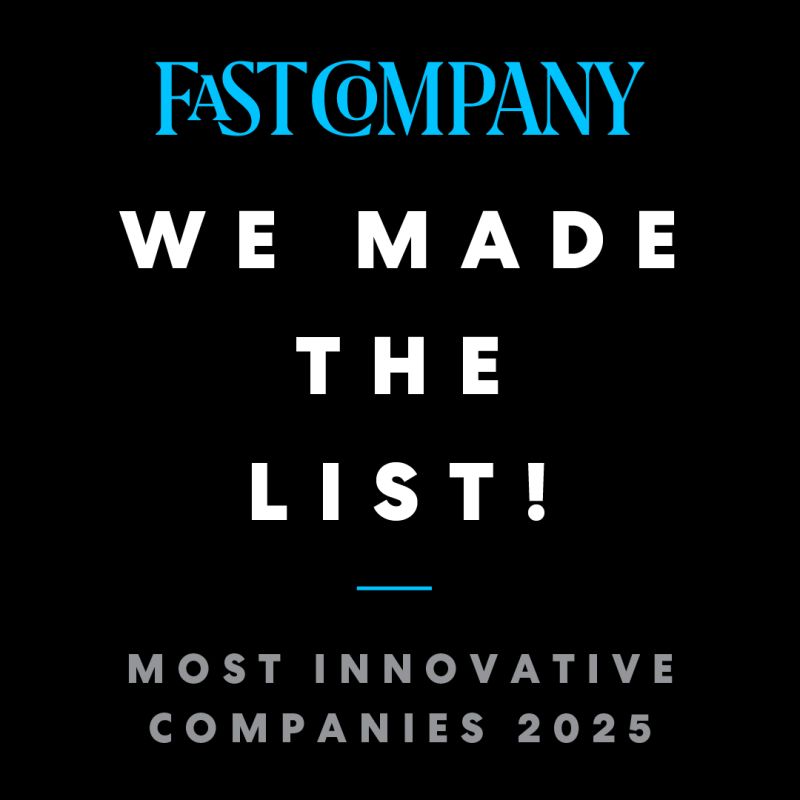
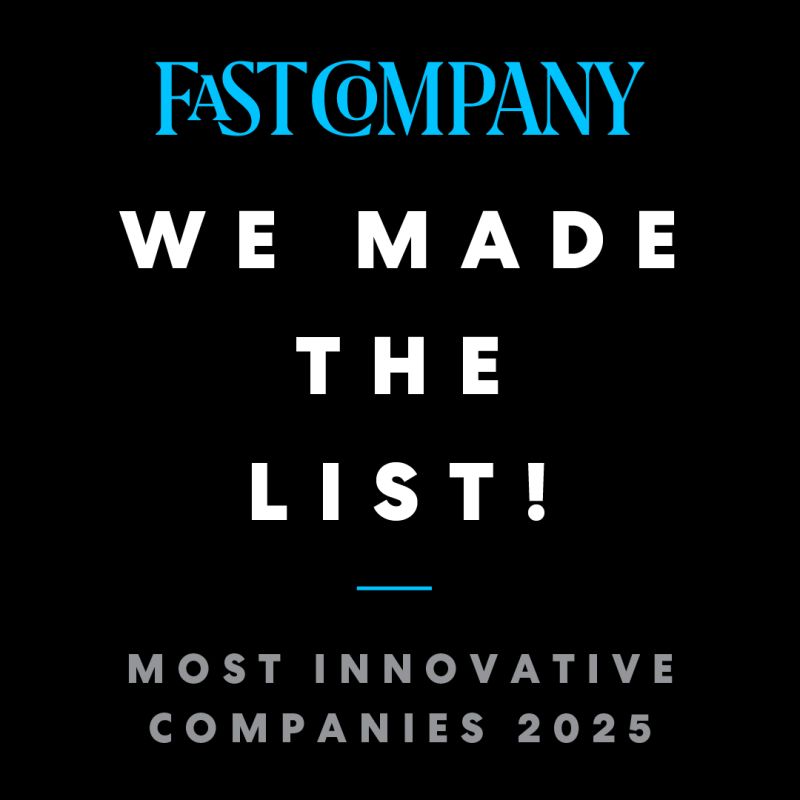
Kojo Named One of Fast Company’s Most Innovative Logistics Companies of 2025
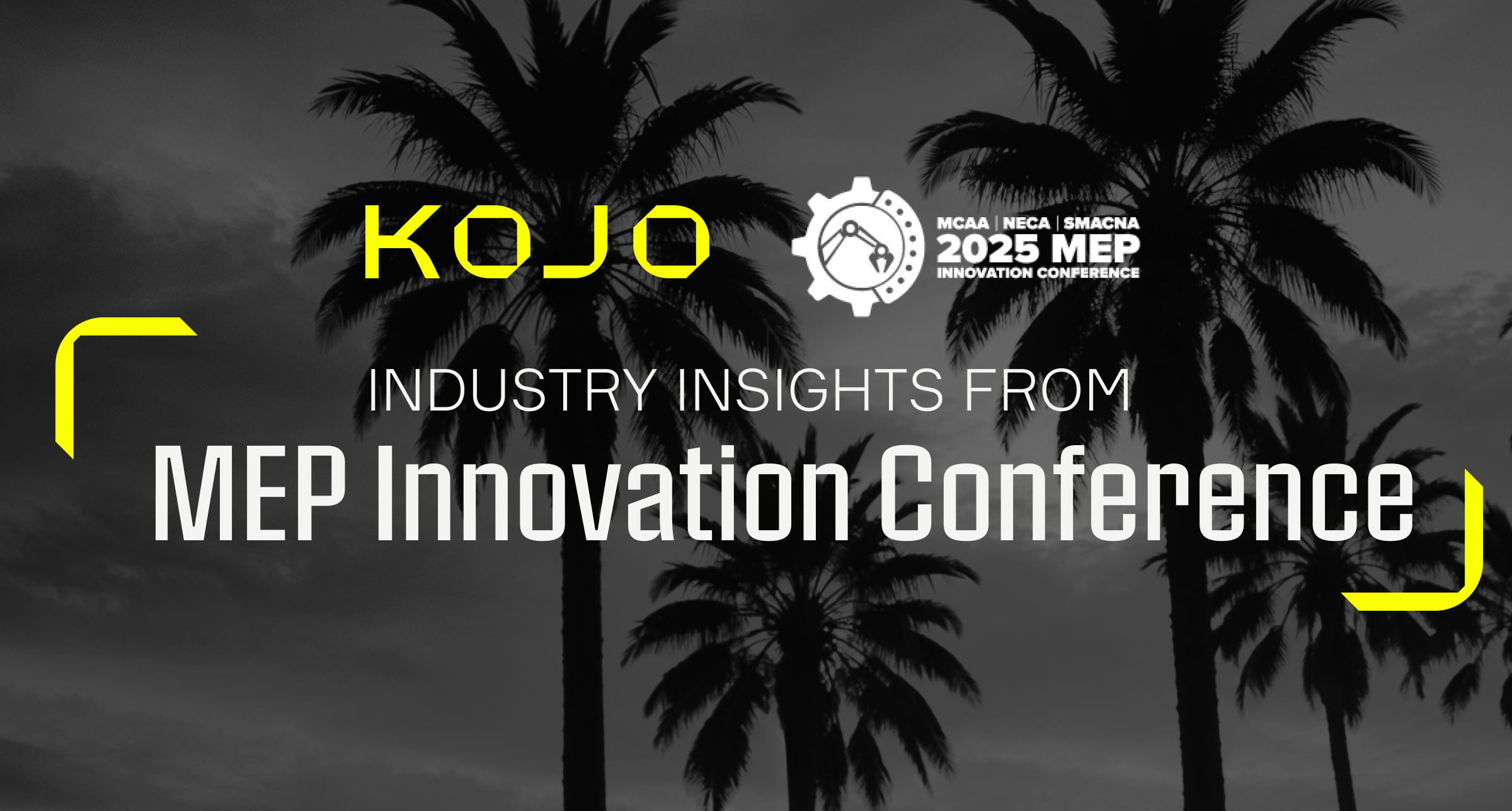
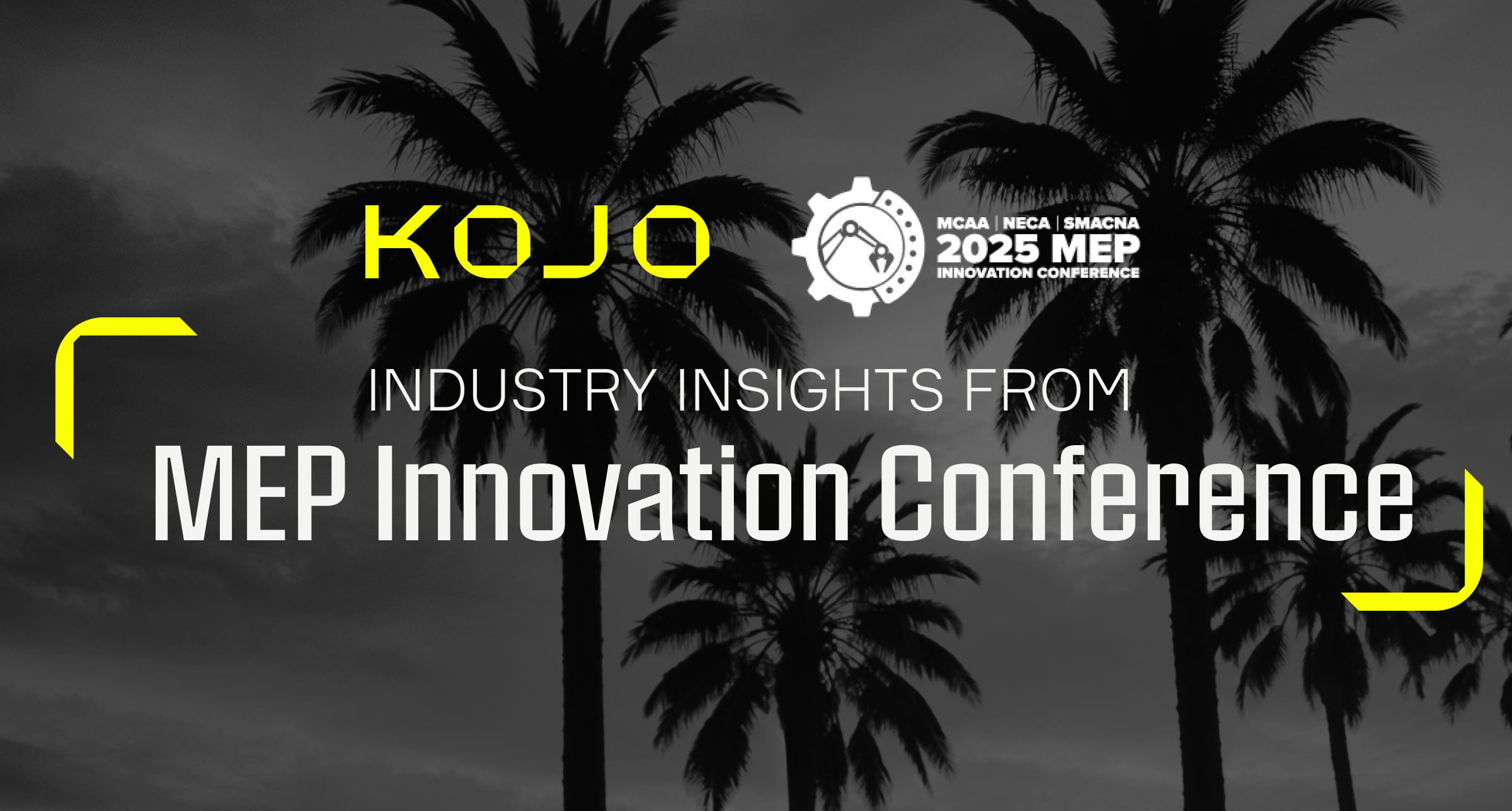
Industry Insights From MEP Innovation 2025: Trends We Observed
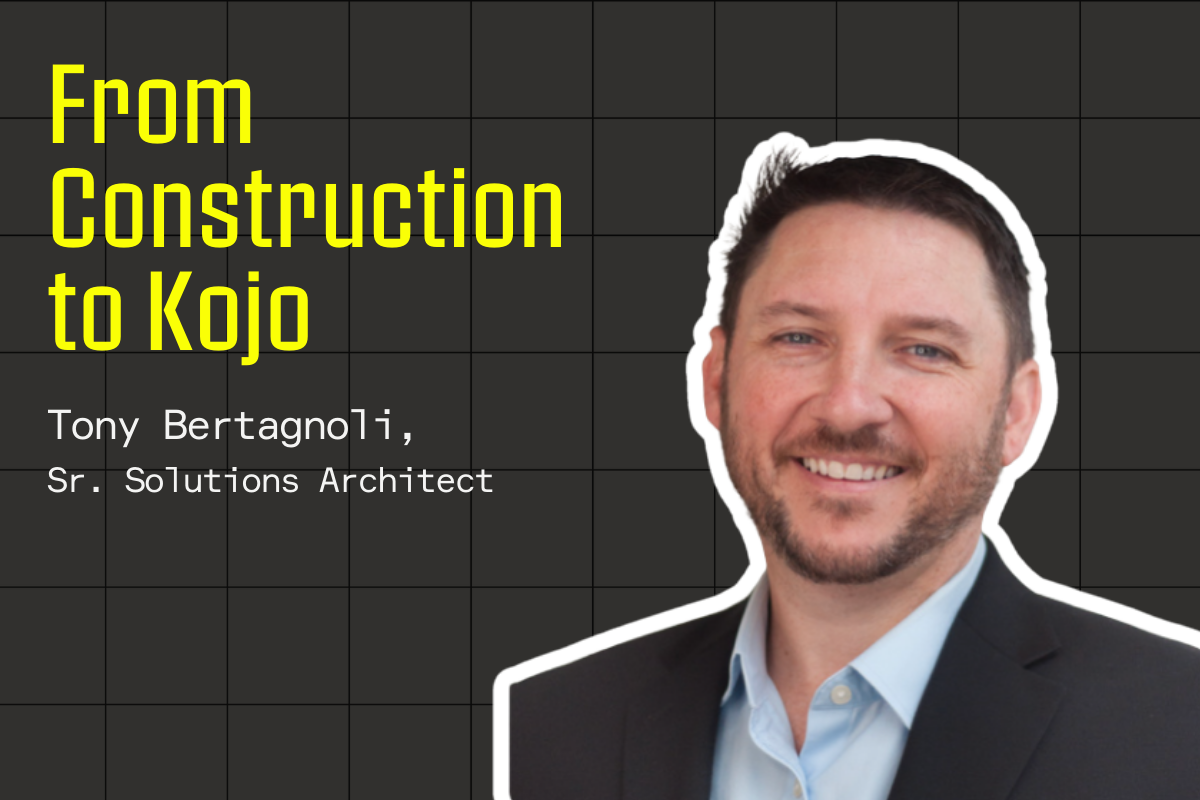
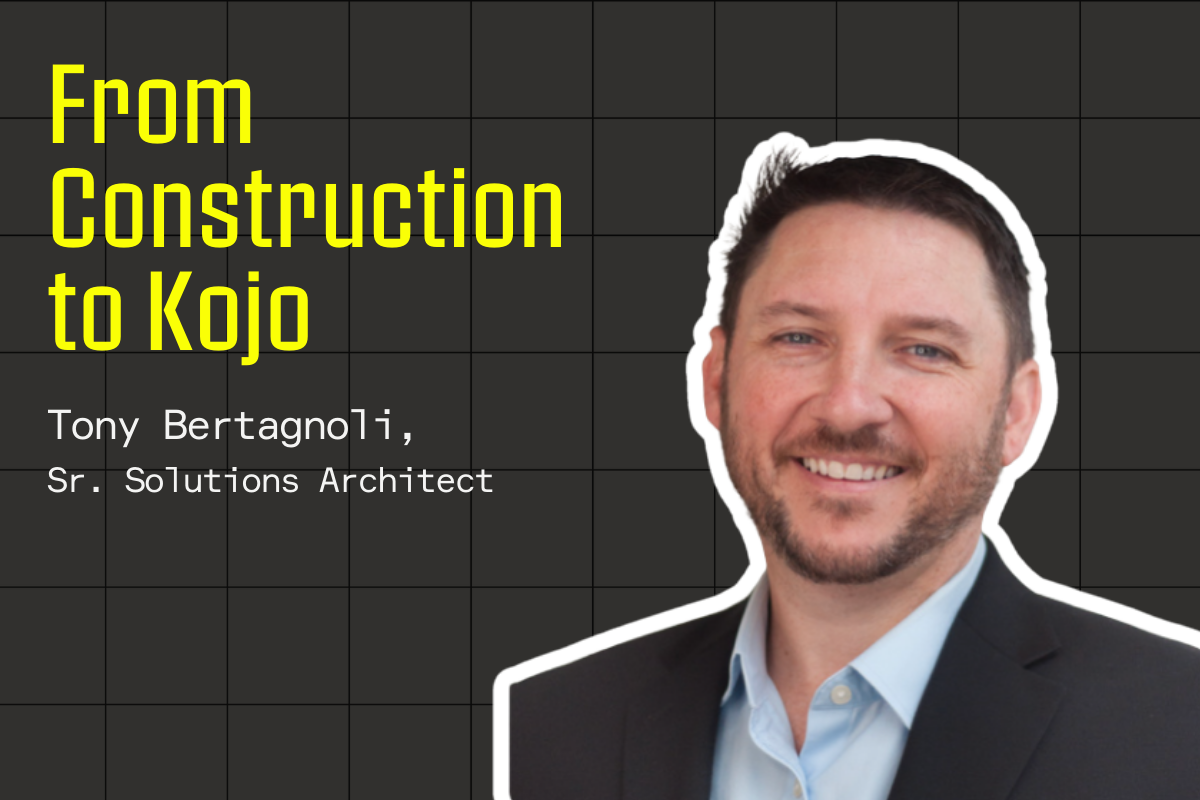